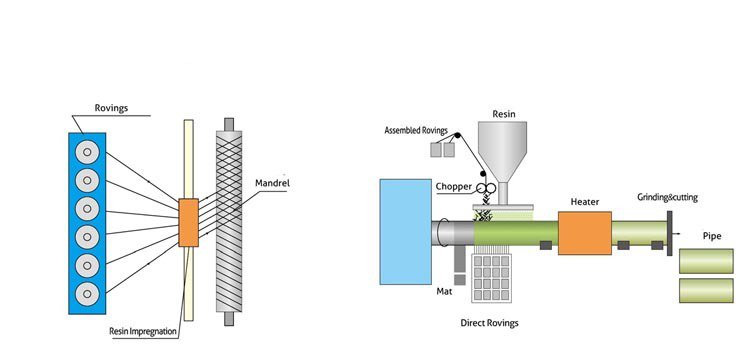
Introduce
As an important advanced manufacturing technology, fiber winding technology is developing rapidly and is widely used in various fields. It uses high-strength fiber materials and winds the fibers on the surface of the workpiece in a specific way through a precisely controlled winding process, thereby giving the workpiece excellent mechanical properties and durability. The emergence of this technology not only promotes technological progress in the manufacturing industry, but also brings new solutions to all walks of life.
In this article, we will discuss the background and significance of filament winding technology, as well as an in-depth analysis of its importance in technological breakthroughs and cutting-edge applications.
Basic principles of fiber winding technology
Fiber winding technology is an advanced manufacturing technology that uses high-strength fiber materials to wrap fibers on the surface of workpieces in a specific manner through a precisely controlled process. Its basic principles cover the filament winding process, material selection and characteristics of filament winding, and equipment and process control of filament winding.
Fiber winding process
The fiber winding process is an advanced manufacturing technology that mainly winds fiber materials on the surface of the workpiece in a specific way, and then impregnates and solidifies them to form a composite structure. According to the different implementation methods of the process and the characteristics of fiber winding, the fiber winding process can be divided into different types, including core mold fiber winding, coreless fiber winding and space fiber winding.
- Filament Winding (FW)
Core die fiber winding is a traditional form of fiber winding process, which mainly includes two types: traditional fiber winding and robotic fiber winding. In the traditional fiber winding process, after the fiber bundle passes through the resin bathtub, the speed of the conveyor and the rotation speed of the mandrel are controlled to pull the impregnated fiber bundle so that it is wound around the mandrel at different angles. The fibers solidify under appropriate time and temperature conditions to form a filament-wound product. Robot fiber winding technology is based on traditional fiber winding technology, using industrial robots to complete fiber winding, and using multi-degree-of-freedom mechanical arms to rotate mandrels or pay-off devices for fiber winding, thereby achieving automation and precision. Production.
- Coreless Filament Winding (CFW)
Coreless fiber winding is a new type of fiber winding technology that does not require a core mold to support fiber winding. The technology was first developed in 2012 by the University of Stuttgart’s Institute for Computational Design (ICD) and the Institute for Building Structures and Structural Design (ITKE). In the coreless fiber winding process, custom-made steel frames or scaffolding are usually used as supports, and anchor points are arranged on these steel frames or scaffolding according to the design requirements of the structure. The robot end effector pulls the resin-impregnated fiber filaments, and then continuously performs fiber winding actions around the frame according to the established fiber winding grammar and robot motion planning path. The fiber material moves back and forth and freely spans between the two anchor points with the robot end effector, and forms a winding node at the anchor point. After impregnation and curing, the final structure is formed with a multi-layer fiber shell.
- Spatial Filament Winding (SFW)
Space fiber winding is developed on the basis of coreless fiber winding. By winding one fiber on another fiber, the entanglement between fibers forms nodes. This interaction between fibers expands the spatial dimensions of fiber winding, allowing components to have more complex geometries and structures. The space fiber winding process requires fibers to move freely in space during the weaving process, so multiple systems are required to work together and be built. Typically, this technology mainly consists of industrial robots and movable gantry, which is mounted with a rigid frame with attached anchor points. The space fiber winding process can create various geometric shapes to form multiple winding nodes within the same frame, and introduces a multi-step solidification process to iteratively manufacture continuous large-scale space frame structures.
Material selection and properties for filament winding
Fiber materials usually include carbon fiber, glass fiber, aramid fiber, etc. Each fiber material has different mechanical properties and chemical properties. For example, carbon fiber has excellent strength and stiffness and is suitable for applications requiring high performance; glass fiber has good corrosion resistance and cost-effectiveness and is suitable for general engineering applications. When selecting fiber materials, factors such as the use environment, performance requirements, and cost of the workpiece need to be comprehensively considered.
Filament winding equipment and process control
It also plays a vital role in the quality and performance of the final product. Fiber winding equipment usually includes winding machines, pretreatment equipment, impregnation equipment, curing equipment, etc. These equipment need to have precise control systems to ensure that parameters such as fiber winding angle, tension, speed, etc. can be accurately controlled to ensure the stability and consistency of the process. In addition, process control also includes the optimization of process parameters, quality inspection and control, etc. to ensure that the final product can meet the design requirements and performance standards.
Technical breakthrough in filament winding technology
With the continuous advancement of science and technology and the changing market demand, fiber winding technology is also constantly innovating and making breakthroughs, providing new possibilities and solutions for applications in various fields.
Application and R&D of high-performance fibers
With the development of fiber material science, more and more high-performance fiber materials are introduced into fiber winding technology to improve the performance and quality of products. For example, high-performance fiber materials such as carbon fiber and aramid fiber have excellent mechanical properties and heat resistance and are widely used in aerospace, automotive industry, sports equipment and other fields. Through continuous research and development and optimization, the application scope of high-performance fibers will be further expanded, bringing new impetus and opportunities to the development of fiber winding technology.
Development of intelligent fiber winding technology
With the rapid development of Industry 4.0 and intelligent manufacturing technology, fiber winding technology is also constantly realizing intelligence and automation. The intelligent fiber winding process realizes real-time monitoring, adjustment and optimization of process parameters by introducing advanced sensors, control systems and artificial intelligence technology, improving production efficiency and product quality. For example, the intelligent control system can achieve precise control of fiber winding angle, tension, speed and other parameters to ensure the consistency and stability of the product. In the future, with the continuous maturity and popularization of intelligent technology, intelligent fiber winding technology will further enhance the level and competitiveness of fiber winding manufacturing.
Exploration of new fiber-wound materials
With the continuous advancement of science and technology and the continuous development of material science, the emergence of new fiber materials has provided new impetus and possibilities for the development of fiber winding technology. For example, the application of new materials such as bionic materials and biodegradable materials will bring new application fields and development directions to fiber winding technology. In addition, the application of new materials such as nanomaterials and smart materials will also bring more possibilities and innovation space to the development of fiber winding technology. Therefore, through continuous exploration and development of new fiber materials, fiber winding technology will further enhance its application value and market competitiveness in various fields.
These breakthroughs will not only promote the development and application of filament winding technology, but also bring more innovation and development opportunities to various industries.
Exploring the cutting-edge applications of fiber winding technology
Application cases in the aerospace field
The application of fiber winding technology in the aerospace field has long become one of the important manufacturing processes, providing lightweight, high-strength and high-performance solutions for spacecraft, aircraft and other flying devices. For example, the outer shell and structural parts of spacecraft are often made of high-strength materials such as carbon fiber or glass fiber through filament winding technology to improve their strength and durability while reducing the overall weight, thus improving carrying capacity and fuel efficiency. In addition, fiber winding technology is also widely used in the manufacture of aerospace engines, such as turbine blades, turbine casings and other key components, to improve their high temperature resistance and fatigue resistance, thereby improving the reliability and performance of the engine.
Fiber Winding Applications in the Automotive Industry
In the automotive industry, fiber winding technology is also widely used in the manufacturing of key components such as body structures, suspension systems, and power transmission systems. By using high-performance fiber materials such as carbon fiber and glass fiber, combined with fiber winding technology, automobile parts can be lightweight and strengthened, thereby improving the fuel efficiency and safety performance of automobiles. For example, car body parts made of carbon fiber reinforced polymer (CFRP) have excellent impact resistance and stiffness, which can effectively reduce the weight of the car body and improve the vehicle’s acceleration and handling performance. In addition, fiber winding technology is also used in the manufacturing of automobile power transmission systems, such as transmission shafts and gearboxes made of carbon fiber, to improve transmission efficiency and durability and reduce the quality and cost of the transmission system.
Innovative applications in the field of medical devices
In the field of medical devices, filament winding technology also shows broad application prospects and innovation space. For example, filament winding technology is used in the manufacture of medical devices such as artificial joints, stents and implants to improve their mechanical strength and biocompatibility, thereby improving treatment effects and patients’ quality of life. By using high-performance fiber materials and precise process control, personalized design and customized manufacturing of medical devices can be achieved to meet the special needs and treatment plans of different patients. In addition, filament winding technology is also used in the outer packaging and protection of medical devices, such as the packaging of medical stents and the fixation of implants, to improve their transportation safety and reliability.
Challenges and future development of filament winding technology
Technical challenges and solutions
Although filament winding technology has shown great potential and advantages in various fields, it also faces some challenges and problems that need to be overcome.
- Improvement of process accuracy requirements.
The success of fiber winding manufacturing often depends on the precise control of process parameters, such as fiber winding angle, tension, speed, etc. However, achieving precise control of these parameters is not easy and requires advanced equipment and precise process control systems, as well as a high level of operating technology and management experience.
- Cost control
While filament-wound manufacturing can achieve lightweighting and increased strength of parts, it is often more costly than traditional manufacturing processes. This is mainly due to the higher cost of fiber materials and process equipment, as well as the higher energy consumption and labor costs in the production process. Therefore, how to reduce the cost of fiber winding manufacturing and improve its economy and competitiveness is an urgent problem that needs to be solved.
Role in sustainable development
Although filament winding technology faces many challenges, it plays an important role in sustainable development. First, filament winding manufacturing has excellent environmental performance. Compared to traditional metal fabrication processes, filament winding manufacturing generally produces less waste and emissions and has a lower environmental impact. Secondly, filament winding manufacturing helps achieve lightweighting, energy saving and emission reduction. By using high-strength, high-stiffness fiber materials, the weight and material consumption of parts can be significantly reduced, thereby reducing energy consumption and carbon emissions, and reducing environmental pressure.
In addition, fiber winding manufacturing can also help improve product life and reliability, reduce maintenance and replacement costs, and provide more reliable technical support for sustainable development.
Future direction
With the continuous emergence of advanced materials and process technologies, fiber winding technology will usher in a wider range of application fields and scope. For example, with the development and application of new fiber materials such as carbon nanotubes and nanofibers, fiber winding technology will show broader application prospects and development space in the fields of electronics, optoelectronics, energy and other fields.
Secondly, the continuous application of intelligent and automated technology will further improve the efficiency and quality of filament winding manufacturing. For example, the application of intelligent control systems and artificial intelligence technology will realize real-time monitoring, adjustment and optimization of the fiber winding process, improve production efficiency and product quality, and reduce production costs and energy consumption.
Finally, the integration of filament winding technology with other advanced manufacturing technologies will further promote its development. For example, the combination with 3D printing technology, bio-manufacturing technology, etc. will enable customized manufacturing of complex structures and functional materials, providing new opportunities and motivation for the transformation, upgrading and innovative development of the manufacturing industry.